Reference
USG recovers 5.6 MW of heat from corrosive flue gases
For USG, the utility provider at Chemelot industrial park, we enabled the reuse of flue gases from the incinerator. These now heat the boiler feedwater in the site's steam network from 20 to 96 °C. With a capacity of 5.6 MW, this results in a major CO₂ reduction.
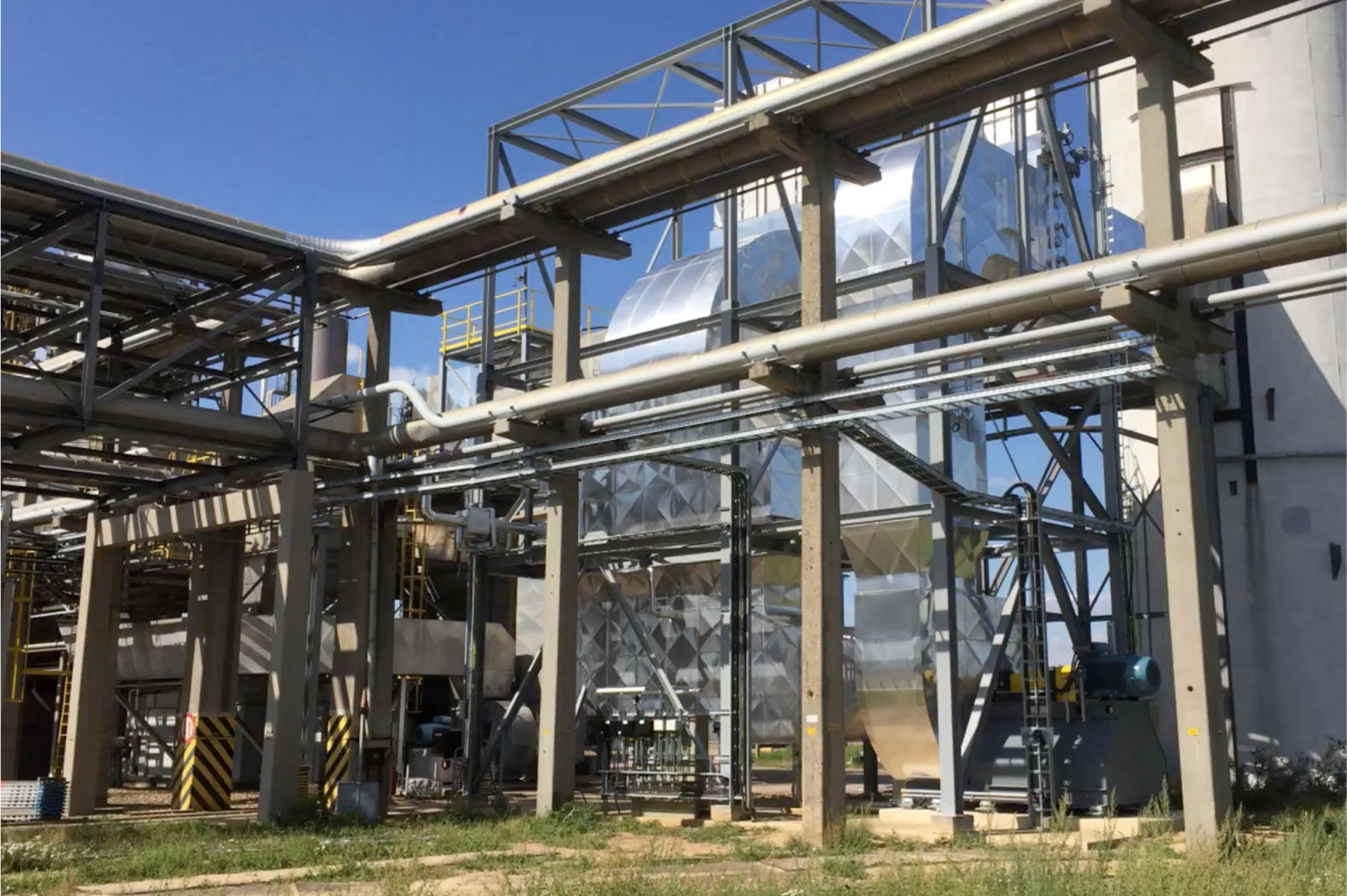
Heat recovery despite corrosive flue gases
USG, the utility provider at the Chemelot industrial park, aimed to reduce its CO₂ emissions. The incinerator appeared to be a promising source of residual heat, ideally suited to preheat the boiler feedwater of the site’s steam network. However, the corrosive nature of the flue gases made heat recovery unfeasible—until Heat Matrix stepped in.
Corrosion-resistant economiser improves efficiency
Heat Matrix designed an economiser with a polymer lining to protect the heat exchanger from acid corrosion. This economiser heats the boiler feedwater from 20 to 96 °C. We created a bypass in the existing ductwork with a dedicated fan, ensuring that the main process is never affected. Depending on the site’s steam balance, the heat recovery system can ramp up, scale down, or temporarily shut off. With a thermal capacity of 5.6 MW, the system delivers significant CO₂ savings.
Specifications
- Operating hours8,400 hrs/year
- Flue gas flow240,000 Am³/hr
- Flue gas temperature157 °C
- Heat exchangerPolymer economiser
- Recovered power5,600 kW
- Energy savings169,344 GJ/year
- CO₂ reduction9,524 tons/year
About project execution, the business case, and working with Heat Matrix
“Potential corrosion problems used to block our efforts to reduce CO₂. Heat Matrix’s polymer economiser solved this challenge.”
Eric Bloemen – Proces Engineer, USG Industrial Utilities
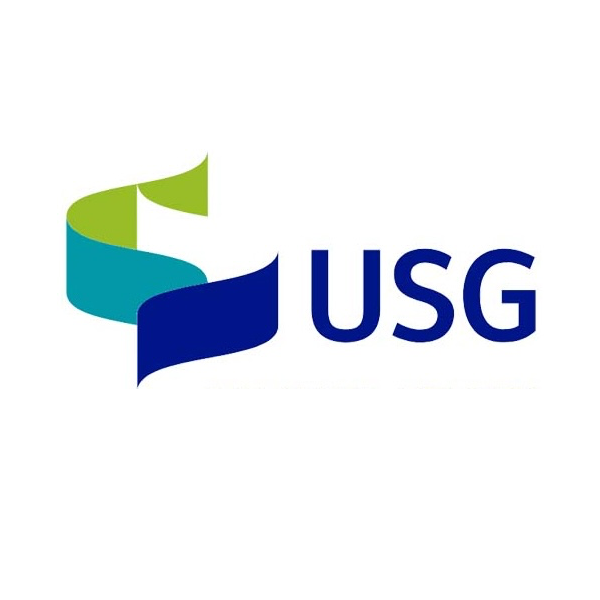
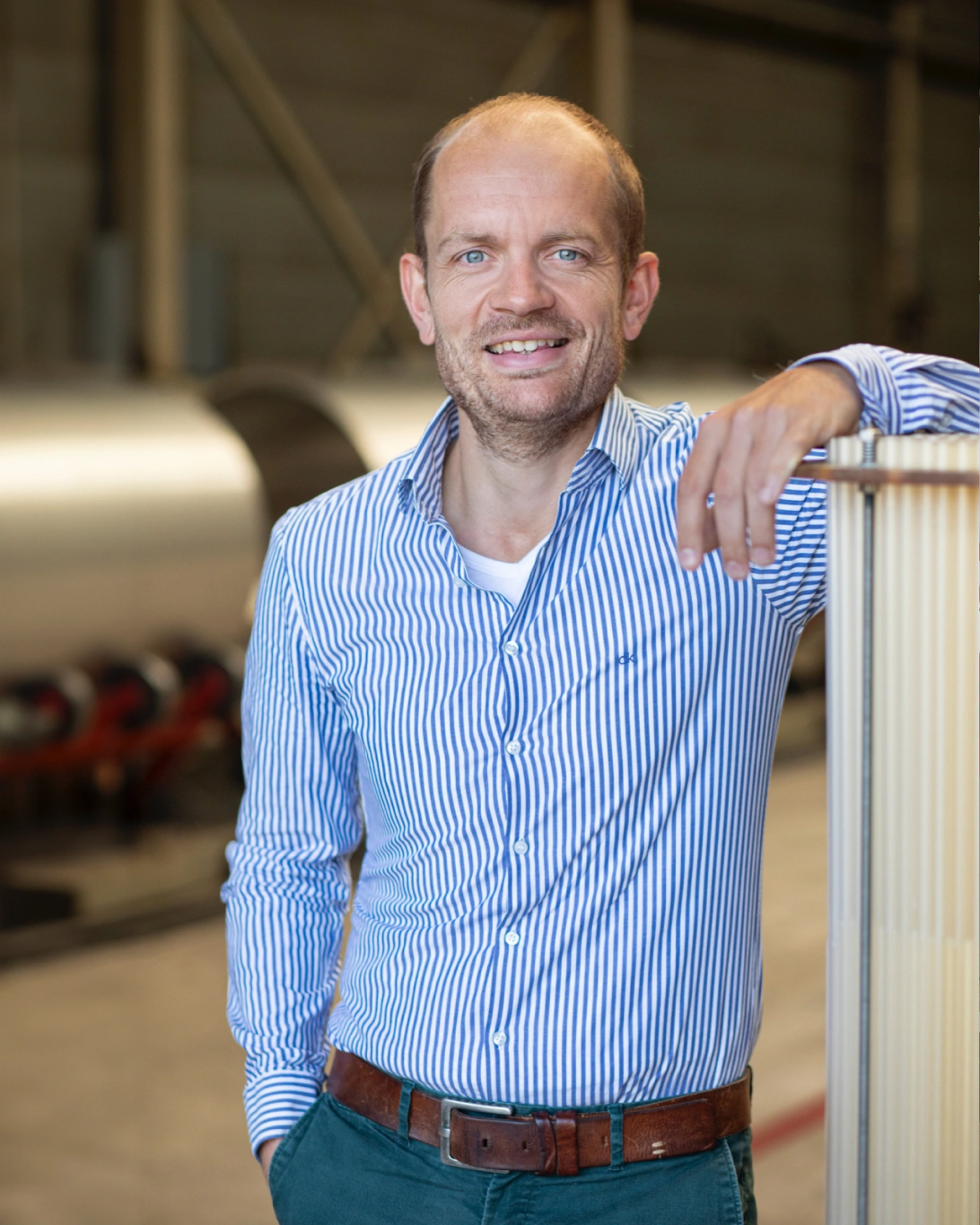
Contact
Curious about your savings potential?
A Heat Recovery Scan gives you quick insight into the most promising concepts for heat recovery, energy savings, reduction of CO2 emissions and payback period.
Related references